What is the Haber-Bosch Process?
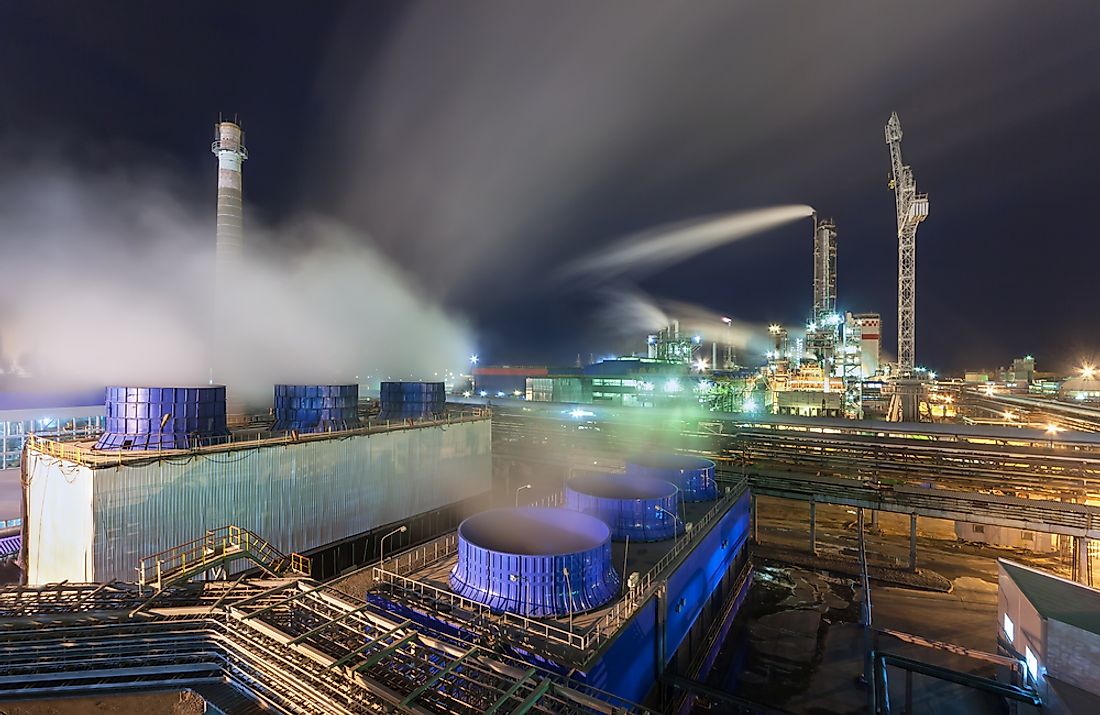
The Haber-Bosch process, or simply the Haber process, is a procedure used in the large scale manufacture of ammonia. This process was named after Fritz Haber and Carl Bosch, the two German chemists who invented the process in the early 20th century. The Haber-Bosch process was developed to replace the less efficient methods that were earlier used in ammonia production such the Frank-Caro process. Today, the Haber-Bosch process is majorly used in the production of the ammonia used in fertilizer, unlike during its invention years when it was used to provide ammonia for explosives that were used in the first war.
Background
The Haber-Bosch process was invented to meet the high demands of ammonia in the 19th century. The ammonia demand rose due to its requirement for fertilizers and livestock food manufacturing. At the start of the 20th century, Haber decided to come up with an alternative method to sustain the demand of ammonia. Haber Fritz, together with his assistant came up with a process that required the use of catalysts and a high-pressured device. The demonstration process was small scale at a laboratory level. The demonstration process took place in the summer of 1909. Ammonia was generated as drops at a rate of 125ml per hour. This process received recognition and was bought by BASF, a German-based chemical company. Carl Bosch was assigned the duty of ensuring the process was upgraded to an industrial level, which he successfully did in 1910. The large scale production of ammonia began in 1913 at the Oppau plant which was owned by BASF. The plant multiplied the production of ammonia which hit 20 tons per day by 1914. The Haber-Bosch process was an asset for Germany during World War I. Haber won a Nobel Prize in 1913 and Bosch won the same prize in 1931.
The Process
Ammonia is formed through a process involving the reaction of nitrogen and hydrogen. The process occurs under temperatures of between 400 and 500 degrees Celsius. Nitrogen and hydrogen gases are passed over catalysts, with constant temperature regulations to keep the equilibrium steady. The gases are passed over four sets of catalysts. At each set, approximately 15% gas reacts to form ammonia. The gases that have not reacted are passed again and again through the catalysts. At the end, almost 97% of the gases have reacted. Nitrogen is not reactive due to the strong triple bonds holding its molecules together. To ensure it reacts with hydrogen, high temperatures and catalysts are required. The hydrogen used in the Haber-Bosch process are mainly acquired from methane. To get hydrogen from methane, steam reforming process is carried out whereby the gas is put under high temperatures and pressure and a nickel catalyst. To increase the rate of production, ammonia produced is frequently removed from the system. The commonly used catalysts in the Haber process include the iron-based catalysts, uranium, and osmium.
Economic and Environmental Aspects
After the Haber-Bosch process was invented, it had to compete with Cyanamide process. The Cyanamide process was ineffective because it utilized large amounts of power and labor. The Haber process has intensified to a level which leads to the production of approximately 450 million tons of nitrogenous fertilizers annually. The large production of fertilizers has led to large tracts of land being put under agriculture. Ammonia fertilizer has increased the agricultural yields and ample food supply, leading to increased population growth rates.