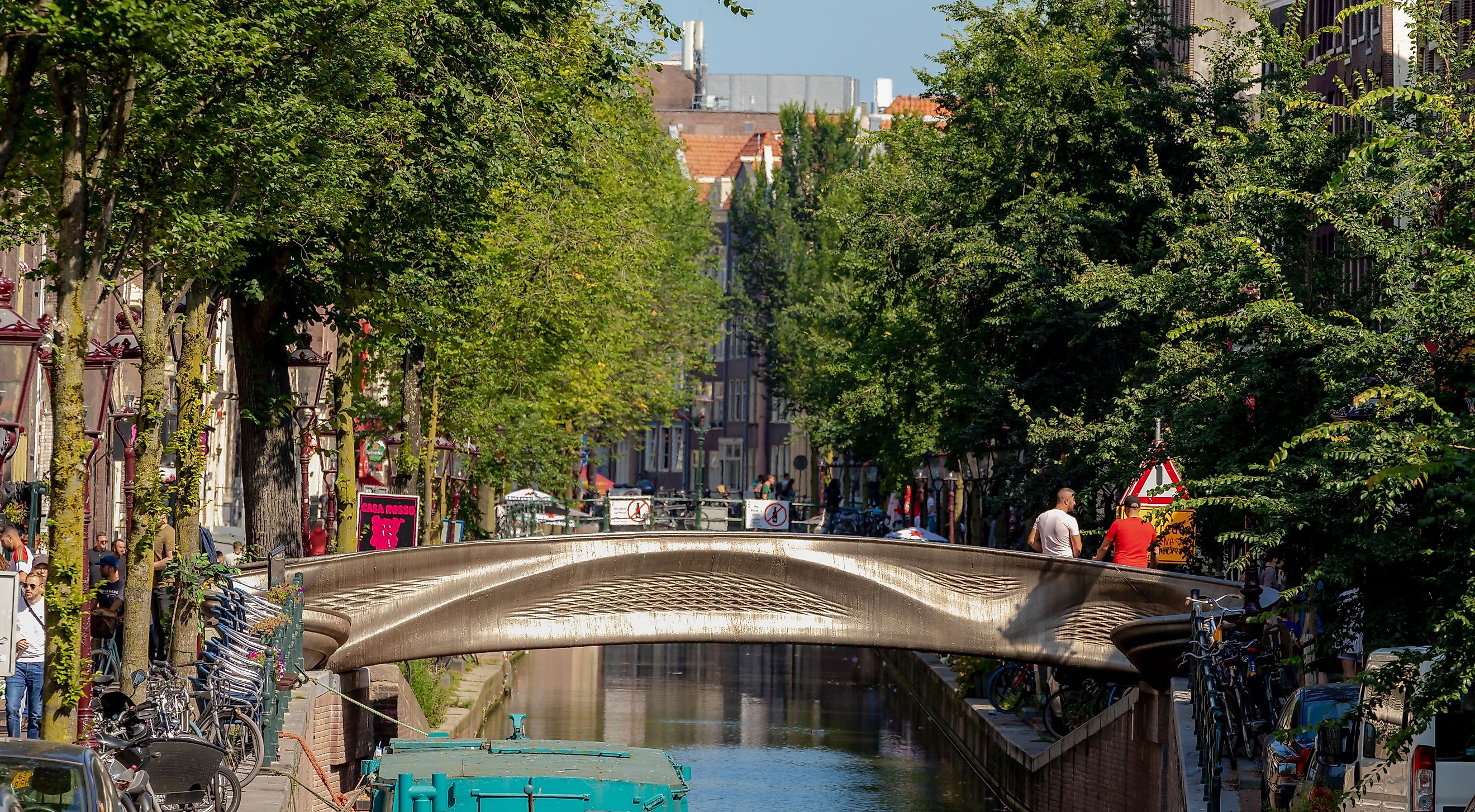
World’s First 3D-Printed Steel Bridge In Amsterdam
In a groundbreaking fusion of art, engineering, and digital technology, Amsterdam now houses the world’s first 3D-printed steel bridge. Unveiled in July 2021 by Her Majesty Queen Maxima of the Netherlands, this 12-meter-long marvel of modern construction stretches gracefully over the historic Oudezijds Achterburgwal canal in the city’s famed Red Light District. It represents not only a significant engineering milestone but also a "living laboratory" for data-driven insights into the performance and longevity of 3D-printed metal structures.
A Marriage of Tradition and Technology
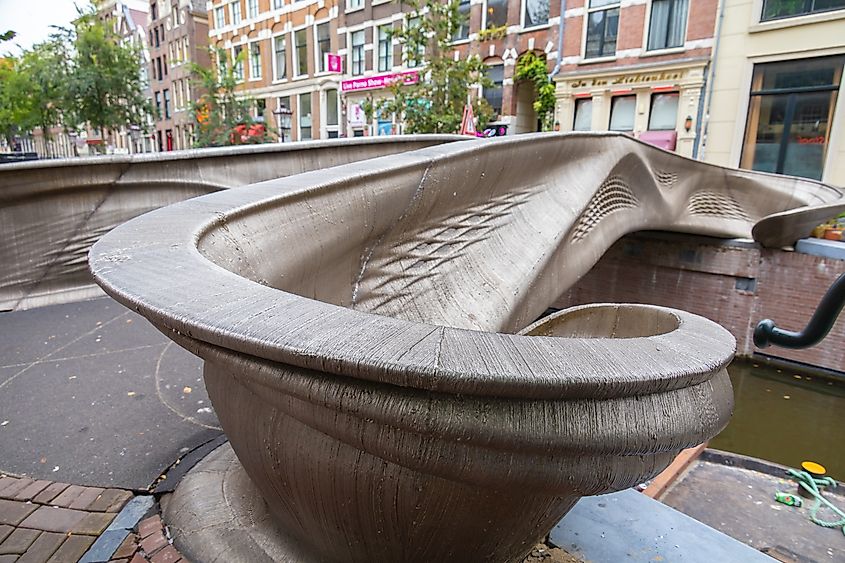
Developed by the innovative Dutch company MX3D, the bridge is the culmination of over four years of collaborative research and development involving architects, engineers, and technologists. At its core, the project integrates advanced digital design with state-of-the-art robotic welding technology—a method that transforms conventional steelwork into an expressive, free-form structure. This revolutionary approach marks a turning point for the construction industry, where traditional methods are increasingly being supplemented by digital design processes and additive manufacturing techniques.
The design journey began with computational design tools, where advanced parametric modeling software such as Grasshopper and Karamba enabled designers to explore an unprecedented freedom of form.
Iterative digital simulations allowed the team to optimize the design by balancing aesthetic appeal with structural integrity. Departing from the conventional U-shaped bridge, the final design evolved into an organic, S-shaped form that marries artistic expression with the rigorous demands of engineering. The bridge’s curved, raw steel balustrades serve as a testament to the dynamic interplay between form and function, reflecting the creative potential unleashed by 3D printing in large-scale urban construction.
Pioneering Research and Robust Testing
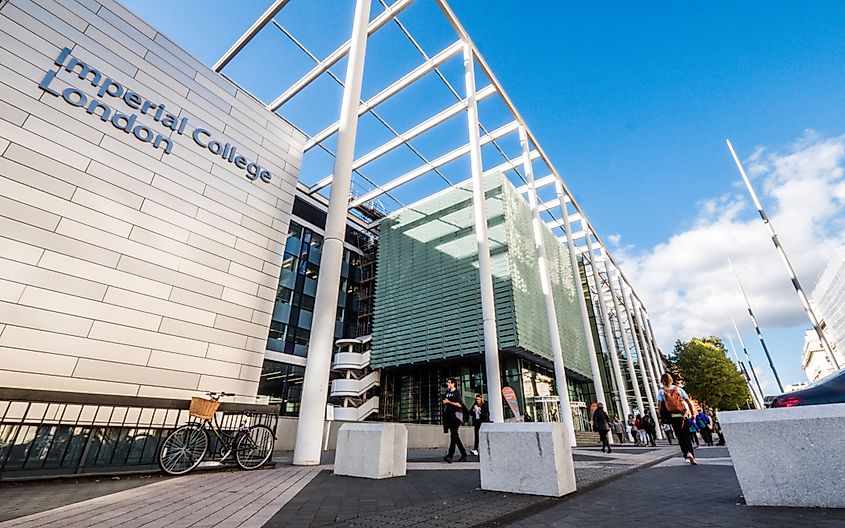
The project is not just a feat of artistic ingenuity; it also represents an important research initiative. Leading the scientific endeavor, the Steel Structures Research Group at Imperial College London undertook extensive testing and simulation work to ensure that the 3D-printed steel could reliably handle the stresses imposed by daily pedestrian traffic. Detailed destructive and non-destructive tests were carried out in state-of-the-art laboratories and on site, confirming the material’s performance and ensuring safety in the absence of established structural design provisions for 3D-printed steel.
Imperial researchers Professor Leroy Gardner and Dr Craig Buchanan played pivotal roles in this process. Professor Gardner remarked, "A 3D-printed metal structure large and strong enough to handle pedestrian traffic has never been constructed before." Meanwhile, Dr Buchanan highlighted the bridge’s significance in transitioning from controlled laboratory experiments to real-world applications. "For over four years, we have been working from the micrometer scale, studying the printed microstructure up to the meter scale, with load testing on the completed bridge," he stated.
Digital Twin Technology: Monitoring the Bridge’s Health
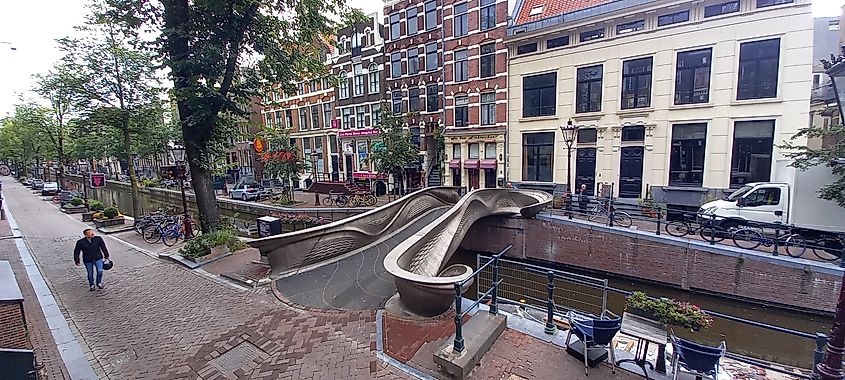
One of the most innovative aspects of the bridge is its integration with digital twin technology. A sophisticated sensor network, embedded within the structure, continuously gathers data on environmental conditions, dynamic loads, and material performance. This information is fed into a real-time digital replica of the bridge—a virtual twin that mirrors its physical counterpart with ever-increasing accuracy. By comparing simulated responses with real-world data, researchers can assess the bridge’s "health" and monitor changes over time. This not only ensures the ongoing safety and maintenance of the structure but also provides valuable insights into the long-term behavior of 3D-printed steel.
Professor Mark Girolami, a leading figure in data-centric engineering from The Alan Turing Institute, commented on the significance of this approach: "When we couple 3D printing with 'digital twin' technology, we can then accelerate the infrastructure design process, ensuring that we design optimal and efficient structures with respect to environmental impact, architectural freedom and manufacturing costs." The collaborative nature of the project is further highlighted by contributions from partners such as Autodesk, ArcelorMittal, ABB Robotics, and TU Delft, among others.
Transforming Urban Landscapes
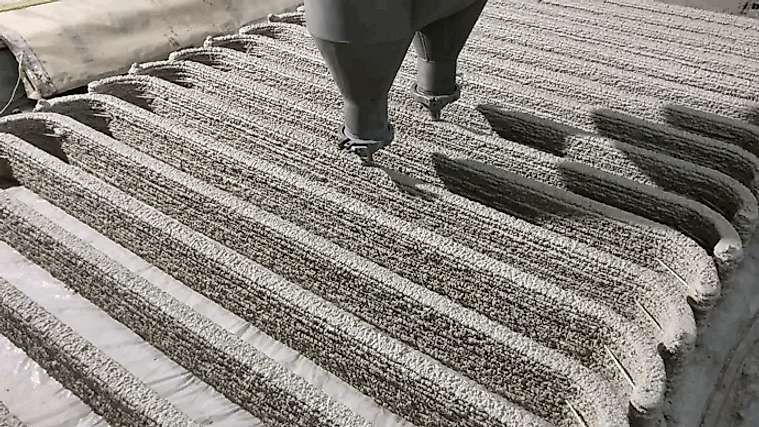
Beyond its technical and research merits, the MX3D bridge symbolizes a new era in urban design and public infrastructure. Traditionally, bridges have been utilitarian in form, designed with uniformity and repetition. However, the freedom afforded by 3D printing and computational design allows engineers and architects to reimagine these structures as works of art. The MX3D bridge challenges conventional aesthetics and inspires new possibilities for how public spaces can be both functional and visually striking.
The bridge’s innovative design also demonstrates significant practical benefits. Additive manufacturing techniques allow for precise material usage, reducing waste and potentially lowering overall construction costs. The ability to print complex geometries directly from digital models streamlines the production process and can substantially cut delivery timelines—a crucial advantage in today’s fast-paced construction environment.
A Collaborative Masterpiece
The creation of the 3D-printed bridge was a true collaborative effort, drawing expertise from multiple disciplines and institutions. The team’s collaborative spirit, spanning structural engineers, mathematicians, computer scientists, and material scientists, has been instrumental in overcoming the challenges inherent in this pioneering project.
Gijs van der Velden, CEO of MX3D, emphasized the importance of collaboration: "We chose to work with Arup, as their experience with innovative projects and generative design were crucial to the project. Our collaboration became even stronger than we expected. Now Arup plays a key role in the co-development of the design method for our metal 3D printing technique." Arup, serving as the lead structural engineer for the project, played a critical role in developing intelligent software that converted welding machines into precise 3D printing robots. Their expertise in generative design was vital in fine-tuning the structure’s geometry, ensuring that the final design met both aesthetic and safety requirements.
Looking Ahead
Now firmly installed in one of Amsterdam’s most vibrant districts, the 3D-printed steel bridge stands as a beacon of innovation and a symbol of what the future of infrastructure might hold. As researchers continue to collect data and refine the digital twin, the insights gained from this living laboratory will inform the design and construction of future projects. The integration of advanced digital tools, real-time monitoring, and sustainable manufacturing practices has the potential to transform not only how bridges are built but also how cities evolve.
In the coming years, the MX3D bridge is expected to influence a new generation of construction projects that prioritize both functionality and creativity. Its success could lead to broader adoption of 3D printing technologies in the construction industry, offering a pathway to more efficient, resilient, and aesthetically compelling infrastructure solutions worldwide.